Essential Warehouse Management Best Practices: Ways To Improve Efficiency
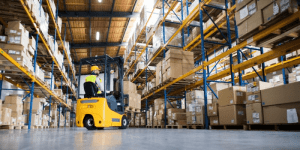
The warehouse can be the place where your elaborate, well-thought-out eCommerce fulfillment strategies go to die. One report found that nearly 30 percent of e-commerce stores cited the warehouse as their top fulfillment challenge. An inefficient warehouse has multiple adverse implications for your business including delays, extra costs, dissatisfied customers, lost/damaged goods, and an outdated inventory.
If there is one thing you want to spend the most time getting right, it is your warehouse process. Let’s take a look at essential warehouse management best practices. From the onset, we must say nothing here will be unfamiliar or groundbreaking. These are all tried and tested principles, some of which have been in use for decades.
Information centralization
The average business runs dozens of applications, and a warehouse is not much different. When information is spread across so many systems, databases, and teams, your staff lacks the global visibility to make the best fulfillment decisions on the fly. A good warehouse management system (WMS) can bridge this disconnect.
It will not replace all your other applications but increases visibility by aggregating relevant information in a single dashboard and pulling key data from other systems. Information centralization creates a single source of truth, makes it easier to monitor inventory levels, and feeds valuable data into ERP or accounting systems.
Automate
Humans make mistakes – lots of them. And it is not necessarily a measure of their competence. We get tired, distracted, and confused, and that’s completely natural. As a warehouse manager, you want to keep this at the absolute minimum. Mistakes are expensive. Customers will not accept that as a reason their order was delayed, misrouted, or misinterpreted.
Automation is the way to go. A 2022 PRG survey found 14 percent of respondents were currently using robotics in their warehouse — an increase from 7 percent in 2021. Create a workflow where manual intervention is greatly reduced. Procure RFID or barcode scanners, conveyors, robots, lift trucks, and more. Make tagging and scanning products as simple as pointing and clicking. These tools should be integrated into your inventory management and/or warehouse management system.
Define picking procedures
Develop a picking process that is easy for workers to follow. This should not be hard for a small warehouse or one processing a few orders. As order volume, variety, and complexity grow, you have to re-strategize to find what works best for your ballooning business.
At the minimum, you should be picking items in waves or batches, as opposed to processing orders individually when they come in. Either way, it’s best to bank on an inventory management system that will help execute the most appropriate picking procedure process.
Minimize touch points
The value of minimal touch points rides on the same principle as warehouse automation — The greater the number of people handling each order, the higher the risk of fulfillment errors and the longer it could take to get to the customer. In one survey, more than half of respondents said they would not purchase from an e-retailer again if their order was misplaced.
If you take a look at all the steps an order goes through before the item leaves the warehouse, you may find that some are not necessary. Certain steps could be a carryover of a legacy process or a workaround that is no longer needed. Each touch point you can get rid of will speed up fulfillment and reduce errors.
Organize products by popularity
If you stock more than one product, the different products will not have identical demand. Likewise, you should not assign them equal space and location priority in the warehouse. Run an analysis of your inventory and categorize items by demand. This analysis should be easy to do with a WMS.
Once done, have the most popular products nearest to packing stations and warehouse exits. Note that product popularity could be seasonal. So this arrangement may have to change from time depending on what’s most popular at a certain period of the year.
Develop and track KPIs
If you are not measuring your progress, you cannot know how well off you are. Develop inventory and fulfillment key performance indicators (KPIs). KPIs do not just show you how well you are doing but are also a means to arrest problems well before they spiral out of control. They also give you a gauge of how well your warehouse is faring against its peers.
Develop a schedule for tracking the KPIs ranging from daily to annually depending on your order volume and the nature of each KPI. The best practice is to track the most critical KPIs on a daily or weekly basis.
Prioritize safety
It’s easy to be caught up in the pursuit of profit and speed to the detriment of the wheel that keeps your entire operation moving – your workers. Yes, warehouse safety is a matter of compliance. But it is much more than that. People’s lives and health are at stake. Meeting the minimum requirement could keep you on the right side of the law but it’s in your interest to hold your warehouse to a higher standard.
Not only does equipment in safer warehouses last longer – employees are happier, more productive, and more loyal. Three in four employees surveyed will join or stay with an employer that prioritizes safety. A good safety record means you spend less on insurance premiums, workers’ compensation, and fighting off bad publicity.
Have contingency plans
Disruptive emergencies will occur – from a cybersecurity breach to a natural disaster. They will have varying degrees of severity ranging from mild to catastrophic. As a business tied to a fixed location, your warehouse should have robust contingency plans that kick in when a disruptive crisis occurs. That way, you can get back to normalcy as quickly as possible.
A good contingency plan should first be proactive than reactive. Spend more time developing measures that prevent a man-made emergency from occurring in the first place. For example, install a reputable anti-malware system to reduce the risk of a cyberattack.
Pursue continuous improvement
Your business, product, market environment, competitors, customers, and regulations are ever-changing. What worked seamlessly a year or two ago might not be the most efficient method today. Your warehouse processes and procedures must evolve in tandem.
In order not to leave the need for such improvement to chance, schedule regular process and procedure reviews. Do it at least once a year. Identify what isn’t working as it should be and then make changes accordingly.
Conclusion
Just because your products get delivered on time and your customers are happy does not necessarily mean your warehouse is running efficiently. There’s a chance that your warehouse has not yet been tested by larger order volumes.
The warehouse management best practices proposed here will make your warehouse run more efficiently today and make it more equipped for when soaring volumes do come in. The result is optimal productivity, time savings, and increased profitability.
—
Alex Selwitz is the Director of SEO for Red Stag Fulfillment, an eCommerce fulfillment warehouse that was born out of eCommerce. He has years of experience in eCommerce and digital marketing. In his free time, Alex enjoys playing guitar and learning about new trends in the digital world.