Order Cycle Time: A Comprehensive Guide to Improving Efficiency in Supply Chain Processes
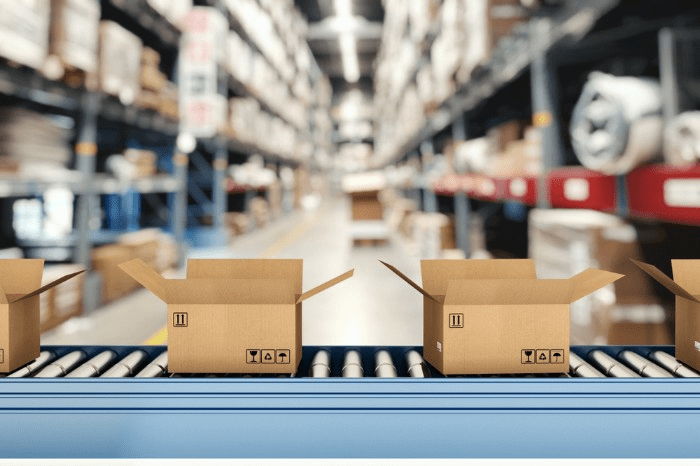
Fulfillment and supply chain professionals know that order cycle time is a key performance indicator for assessing the success of their operations. In an industry where customer satisfaction depends on efficient order fulfillment, it is essential to reduce lead times and optimize production processes. This article looks at how businesses can use technology to reduce order cycle time and improve efficiency in the supply chain process. We will discuss the importance of order cycle time management, the advantages of leveraging technology to optimize fulfillment centers and processes, and how Cadre Technologies software can help companies achieve their goals.
What is Order Cycle Time?
Order cycle time is a critical metric in supply chain management that measures the time it takes to process an actual order, from the time the order is received until the order is handed off to a carrier for shipment. It is an essential factor in customer satisfaction and retention and overall business success. Order cycle time can vary based on several factors, including the complexity of the order, the number of orders received, and the type of product being ordered. The faster the order cycle time, the more orders can be processed, resulting in increased productivity and profitability.
Customer Order Cycle Time vs. Fulfillment Order Cycle Time
Traditionally, order cycle time is defined as the time it takes to fulfill a customer order, from the time the order is placed to the time the customer receives the order. However, in the fulfillment industry, the definition is slightly different. It is defined as the time the order is received until the order is handed off to a carrier for shipment. This definition is more appropriate for the fulfillment industry because it accounts for the entire process of fulfilling an order, including processing, packing, and shipping.
Calculating Order Cycle Time in Fulfillment
As mentioned, order cycle time is an important metric for measuring the efficiency of the order fulfillment process. It is the time it takes for a fulfillment provider to process and fulfill an order, from the time it is received until it is handed off to a carrier for shipment. Calculating the order cycle time can help businesses identify areas for improvement and make data-driven decisions to optimize their fulfillment process.
To calculate the order cycle time, follow these steps:
1. Determine the period of time for which you want to calculate the order cycle time. This could be a day, week, or month, depending on your business needs.
2. Determine the total number of orders fulfilled during the selected time period.
For example, let’s say a fulfillment provider shipped 2,000 orders during a 24-hour period.
3. Determine the total amount of time spent fulfilling orders during the selected time period.
This includes the time it takes to receive the order, process the order, pick and pack the items, and hand off the order to a carrier for shipment. To calculate this time, you can use a time tracking system or manually record the start and end time for each order.
For example, let’s say the total time spent fulfilling orders during the 24-hour period was 20 hours.
4. Use the following formula to calculate the order cycle time:
(total time spent fulfilling orders) * (3600 [number of seconds per hour]) / (total number of orders shipped) = average cycle time
For example, using the numbers from above:
(20 * 3600) / 2000 = 36 seconds per order
So the average order cycle time for this fulfillment provider during the 24-hour period was 36 seconds per order.
It’s important to note that this calculation only takes into account the time it takes for a fulfillment provider to process and fulfill an order, and does not include the time it takes for the order to be delivered to the customer.
Why is Order Cycle Time Important?
Order cycle time is important because it is a critical factor in meeting customer expectations for fast and reliable delivery times. Failure to meet customer expectations can lead to negative feedback, increased costs due to returns, and lost revenue.
Additionally, a shorter order cycle time means more orders can be processed, resulting in increased productivity and profitability. Late deliveries and order inaccuracies can negatively impact the customer experience and harm your reputation as a fulfillment provider.
How to Improve Order Cycle Time
Improving efficiency in the order fulfillment cycle time involves identifying bottlenecks and developing strategies to address them. Here are some ways to improve order cycle time:
Optimize Fulfillment Centers
Efficient fulfillment centers can help reduce the time spent on picking, packing, and shipping orders. Companies can use an automated system that prioritizes orders based on their due date to ensure that orders are processed and shipped on time. This can include the use of technology such as a Warehouse Management System, RF scanning, and robotics.
Batch Processing
Batch processing involves processing multiple orders simultaneously. This process can save time on traveling within the warehouse, resulting in faster order processing times. A Warehouse Management System can group orders and prioritize them based on shipping times, destination, carrier, etc.
Efficient Order Management Process
Efficient order management can reduce the time it takes to pick and pack orders. Companies can use a real-time inventory system that tracks raw materials and finished goods to ensure that they have the necessary items to fulfill customer orders.
Streamlined Order Fulfillment Process
The order fulfillment process should be streamlined to minimize order cycle time. Companies can use automation to speed up the process, reducing the time it takes to produce finished goods and reducing the time it takes to hand off orders to a carrier for shipment. Through the use of barcodes and RF scanning, you can eliminate errors from manual entry, decrease picking times, and have real-time visibility into inventory counts.
Partner with Reliable Carriers
Partnering with reliable carriers can reduce shipping delays and ensure that your shipments can be handed off on time so that customers receive their orders on time. Companies should use carriers that offer real-time tracking and reporting to manage the entire delivery process effectively.
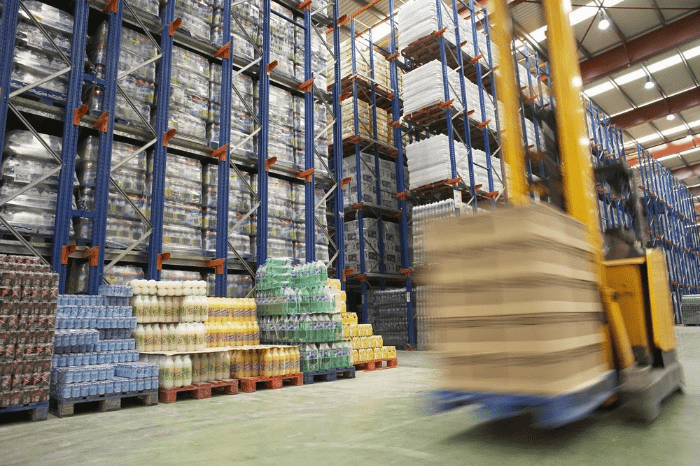
Cycle Time and Lead Time
Lead time and order cycle time are two supply chain metrics that can impact order fulfillment efficiency. Lead time refers to the time it takes to receive raw materials, produce finished goods, and hand off orders to a carrier for shipment.
In contrast, order cycle time refers to the time it takes to process an actual order. The order cycle time formula only takes into account the time between the order placement date and the carrier handoff date.
Customer Order Cycle Time
Customer order cycle time is the time it takes for a customer to receive their order after placing it. While this is a separate metric from order cycle time for fulfillment providers, it is still important to consider in the overall order fulfillment process. A shorter customer order cycle time means that companies can meet customer demand more efficiently.
To calculate customer order cycle time, businesses should measure the time between the customer’s order date and the delivery date. This metric can be used to gauge how quickly customers are receiving their orders and adjust strategies accordingly.
Importantly, businesses should record the total number of orders shipped and the average time to fulfill orders to identify areas for improvement in the overall fulfillment process.
Managing Customer Expectations
Managing customer expectations is critical for fulfillment providers. Setting realistic delivery timeframes based on order cycle time and lead time can help prevent negative feedback and increase customer satisfaction. Clear communication throughout the order management process can also help set expectations, manage delays, and maintain satisfied customers. Online shoppers expect to receive updates on the status of their orders, such as shipping notifications and tracking numbers.
Reducing Supply Chain Disruptions
Supply chain disruptions, such as late deliveries and shipping delays, can have a significant impact on order cycle time. Companies should take steps to minimize disruptions, such as identifying alternative suppliers, maintaining safety stock, and having a backup plan in case of unexpected events. Additionally, having real-time visibility into the status of orders can help companies proactively address potential disruptions and improve order cycle time.
How to Keep Lead Times to a Minimum
Keeping lead times to a minimum can help reduce order cycle time and improve customer satisfaction. Here are some ways to keep lead times to a minimum:
Just-In-Time Inventory Management
Just-in-time (JIT) inventory management involves only ordering and receiving inventory when it is needed, reducing the amount of time spent in inventory storage. This can help reduce lead times and improve order fulfillment efficiency.
Partnering with Reliable Suppliers or 3rd Party Logistic (3PLs)
Partnering with reliable suppliers can reduce the time it takes to receive raw materials and finished goods. Companies should work with suppliers that can provide fast and reliable deliveries to meet customer demand. If using a 3PL, the 3PL must be efficient in their receiving and shipping operations or it will reflect poorly on you.
Optimizing Production Processes
Efficient production processes can reduce lead times by speeding up the time it takes to produce finished goods. Companies can use automation, such as robotics and artificial intelligence, to improve efficiency and reduce the time it takes to manufacture products.
Tracking and Monitoring Lead Times
Tracking and monitoring lead times can help identify areas for improvement. In the manufacturing process as well as for fulfillment providers who perform value-added services such as kitting, companies can record the time it takes to receive raw materials, produce finished goods, and hand off orders to carriers for shipment to identify bottlenecks in the supply chain.
Cadre Technologies Software for Order Cycle Time Management
At Cadre Technologies, we offer software solutions that can help businesses optimize their order cycle time, reduce lead times, and improve efficiency in their supply chain process. Our software includes:
- Warehouse management, order management, and transportation management features that can be customized to meet the specific needs of different businesses.
- Real-time tracking and reporting on order status, inventory levels, and other supply chain metrics.
- Automated tasks such as inventory management, order processing, picking and packing, and shipping to improve efficiency in the order fulfillment process.
Cadre Technologies software can help businesses:
- Reduce order cycle time by streamlining the entire order management process, from order receipt to carrier handoff.
- Implement features such as batch processing, order prioritization, and real-time inventory tracking to reduce the time it takes to fulfill customer orders.
- Manage customer expectations by providing real-time updates on order status, delivery times, and other information related to order fulfillment.
- Improve order accuracy and meet customer demand by providing real-time visibility into the status of orders and potential supply chain disruptions.
Conclusion
In conclusion, order cycle time is a critical key performance indicator for fulfillment providers that measures the time it takes to process and fulfill an order, from the time it is received to the time it is handed off to a carrier for shipment. By optimizing fulfillment centers, streamlining the order fulfillment process, partnering with reliable carriers and suppliers, and managing customer expectations, businesses can reduce order cycle time, improve efficiency, and increase the satisfaction of your customers.
By leveraging technology such as Cadre Technologies software to automate tasks and provide real-time visibility into the order fulfillment process, businesses can achieve greater efficiency, reduce costs, and meet customer demand more effectively.
If you’re looking to optimize your order cycle time and improve your fulfillment process, consider implementing Cadre Technologies Warehouse Management software. Contact us today to learn more about how we can help you achieve your business goals.